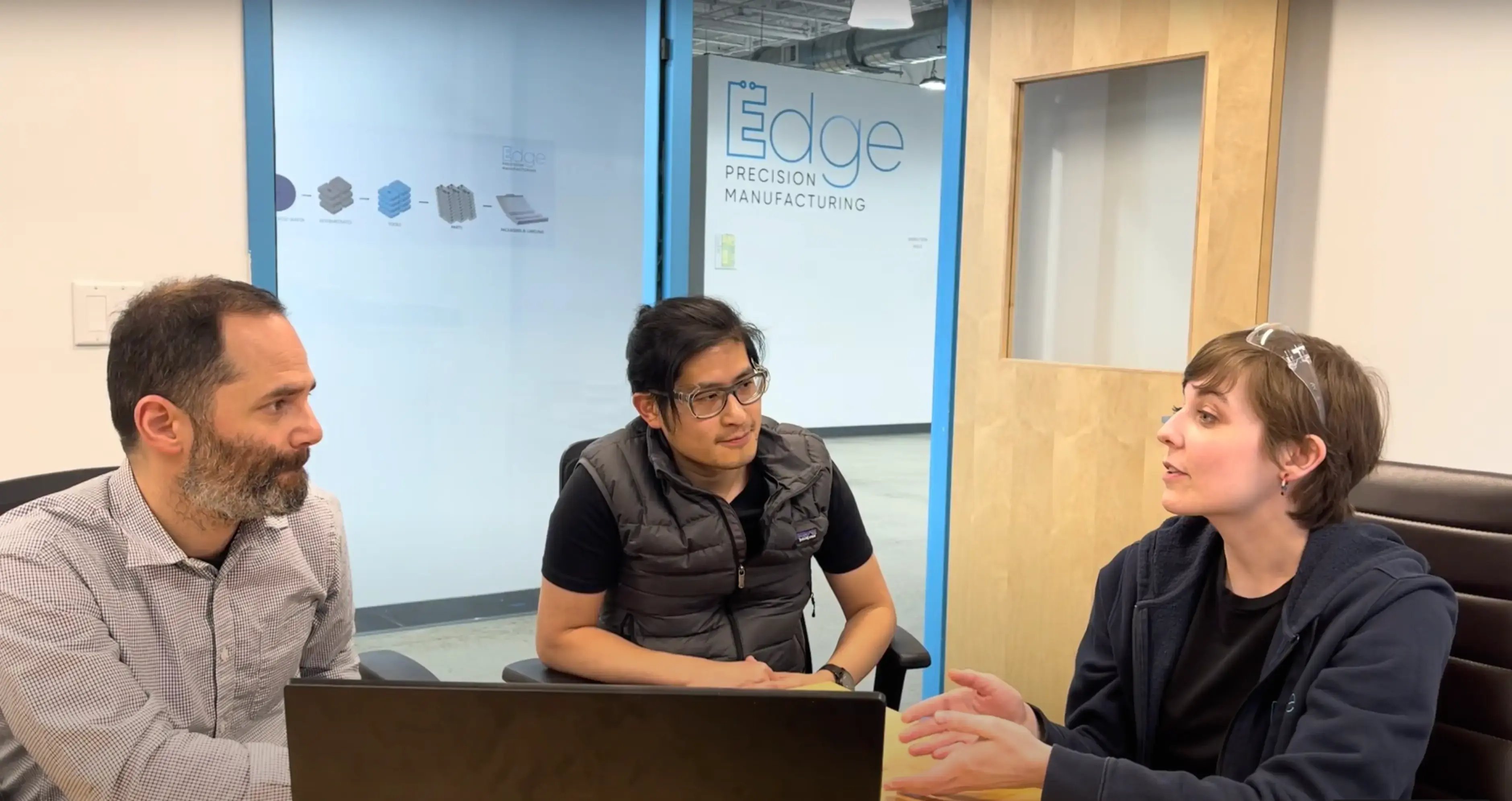
Customer Success Stories
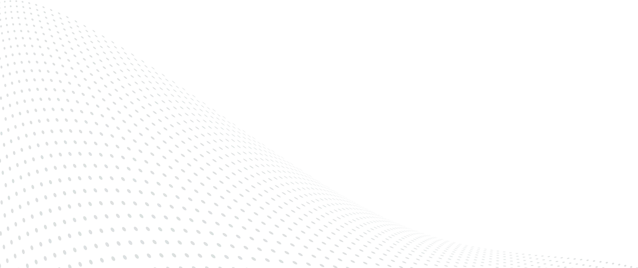
Edge’s technology enables next-generation products
Explore our featured projects to see how Edge’s expertise and teamwork help our customers succeed. We encourage you to scroll through the projects to explore the details and solutions
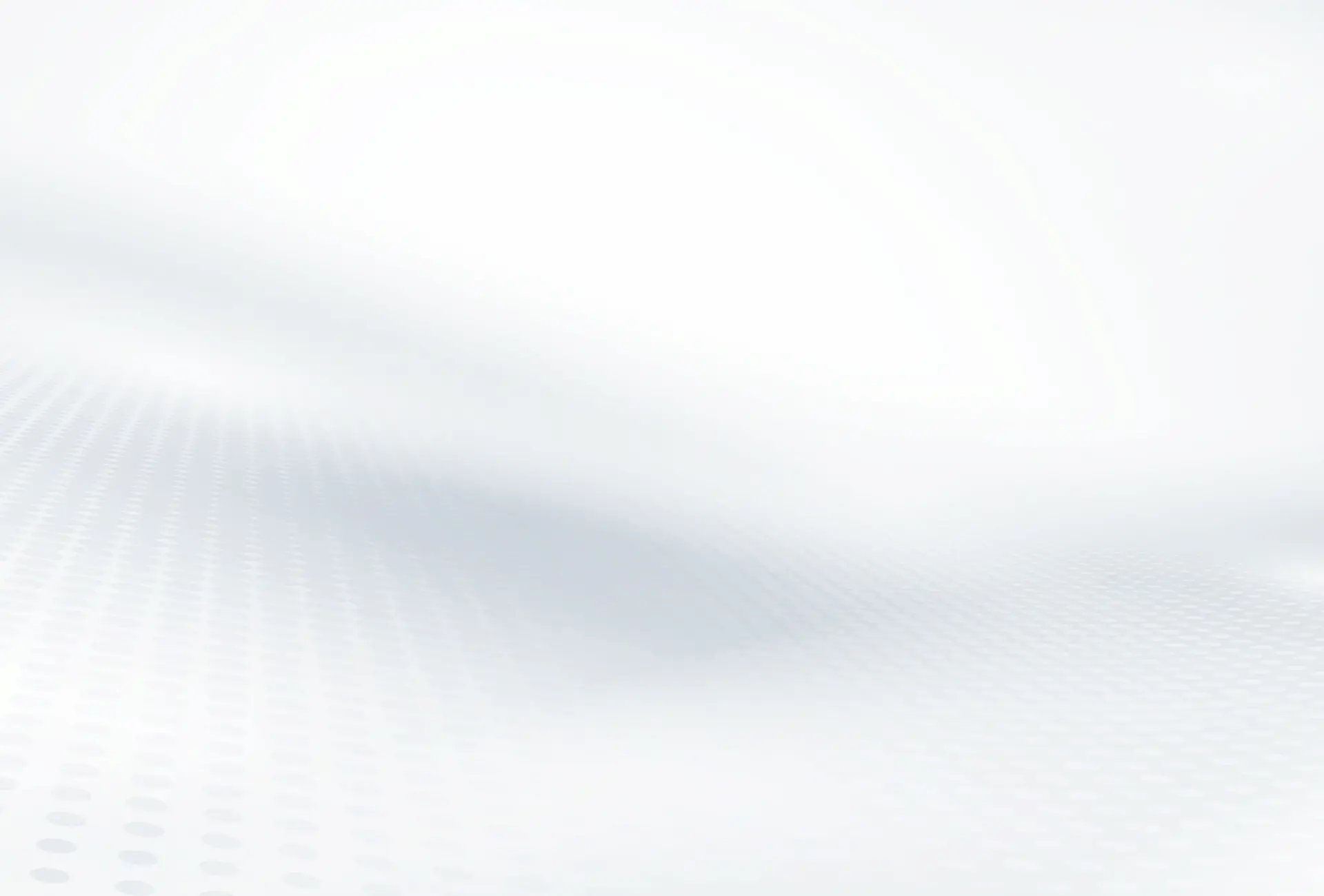
Cell and gene therapy (CGT) device for white blood cell separation from whole blood
Designed for commercial release, the CGT medical device required sophisticated components to separate white blood cells from whole blood, principally:
- Extremely large parts of dense micropost arrays within a highly parallelized microfluidic device
- Micropillar arrays used to filter white blood cells out from red blood cells, platelets, and other plasma components in preparation for downstream transfection
Edge was the only vendor that provided a cost-effective solution for offering a high-aspect-ratio structure and plastic.
- Edge fabricated multiple design iterations during product development, including testing with different thermoplastic materials and geometries
- Edge took the product through full validation under 21 CFR 820 and ISO 13485 requirements
- Edge manufactures the product in an ISO Class 7 cleanroom, suitable for use as a disposable medical device
_whatwecandoforyou.webp?width=1260&height=1260&name=Cell_and_gene_therapy_(CGT)_whatwecandoforyou.webp)
Circulating tumor cell isolation device
Developed by a leading domestic biotech company, a circulating tumor cell device with a backbone manufactured by Edge is currently on the market.
The device requires:
- Sub-micron feature precision across tens of thousands of features
- Minimal birefringence and low background fluorescence for imaging application
- Tightly controlled flatness spec across the entire part for z-height focal plane consistency
As a supplier to the biotech company for more than a decade, Edge has:
- Provided the core backbone of the device, which a third-party vendor incorporates into a full kit with reagents and instructions for use (IFU)
- Consistently produced the precision parts without once requiring tool replacement
- Refined inspection and sampling requirements to optimize production for cost reduction, with no decrease in quality
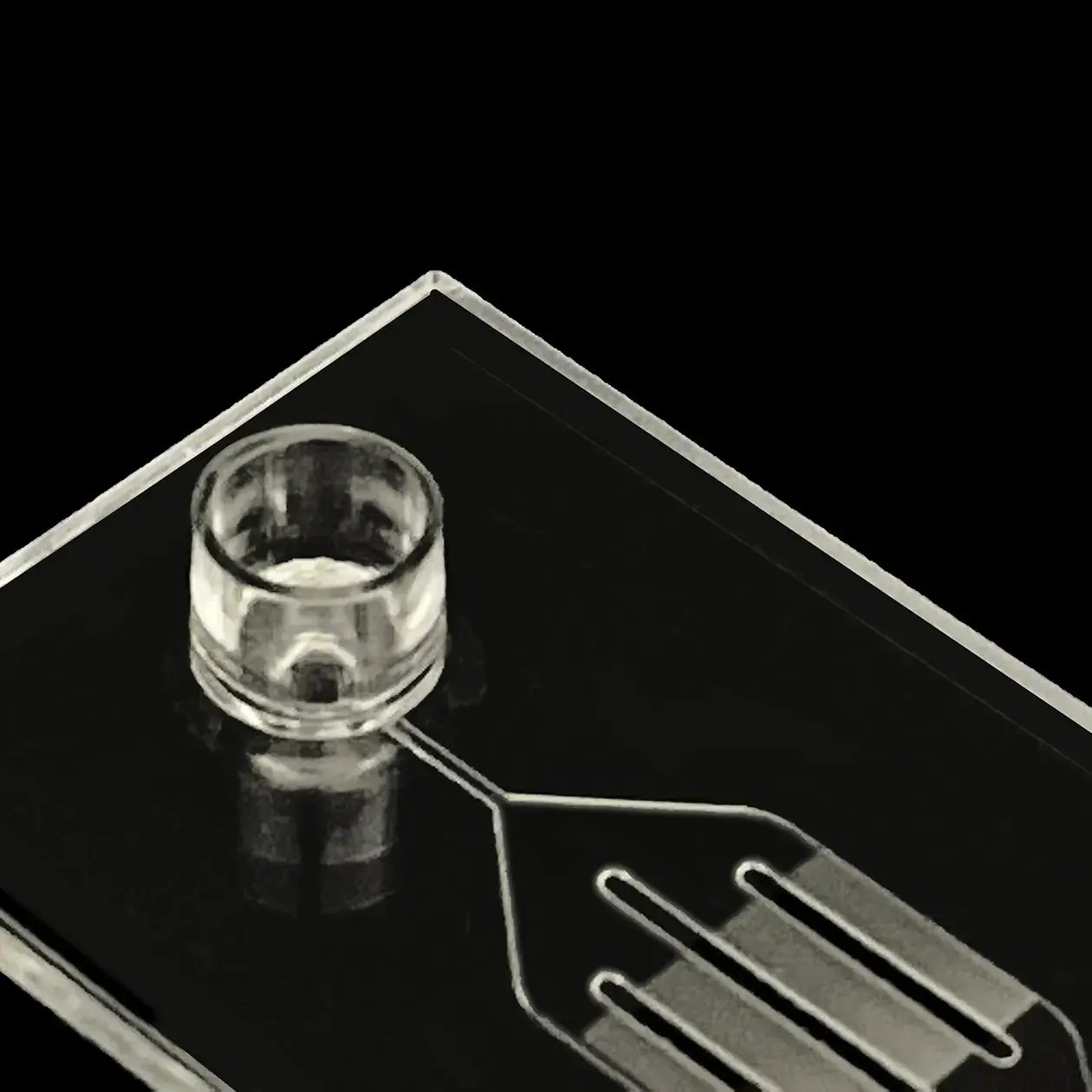
Thermal compression molding to correct manufacturing defects in existing part
A customer was experiencing significant manufacturing issues with an existing and available product. Traditional injection molding processes led to the part:
- Developing significant internal stresses
- Cracking during laser welding and ultrasonic welding
Using thermal compression molding, Edge:
- Replicated the existing part with far superior optical and geometric performance
- Produced parts with far less internal stress
- Eliminated cracking and increased the shelf life of the customer’s fully assembled devices
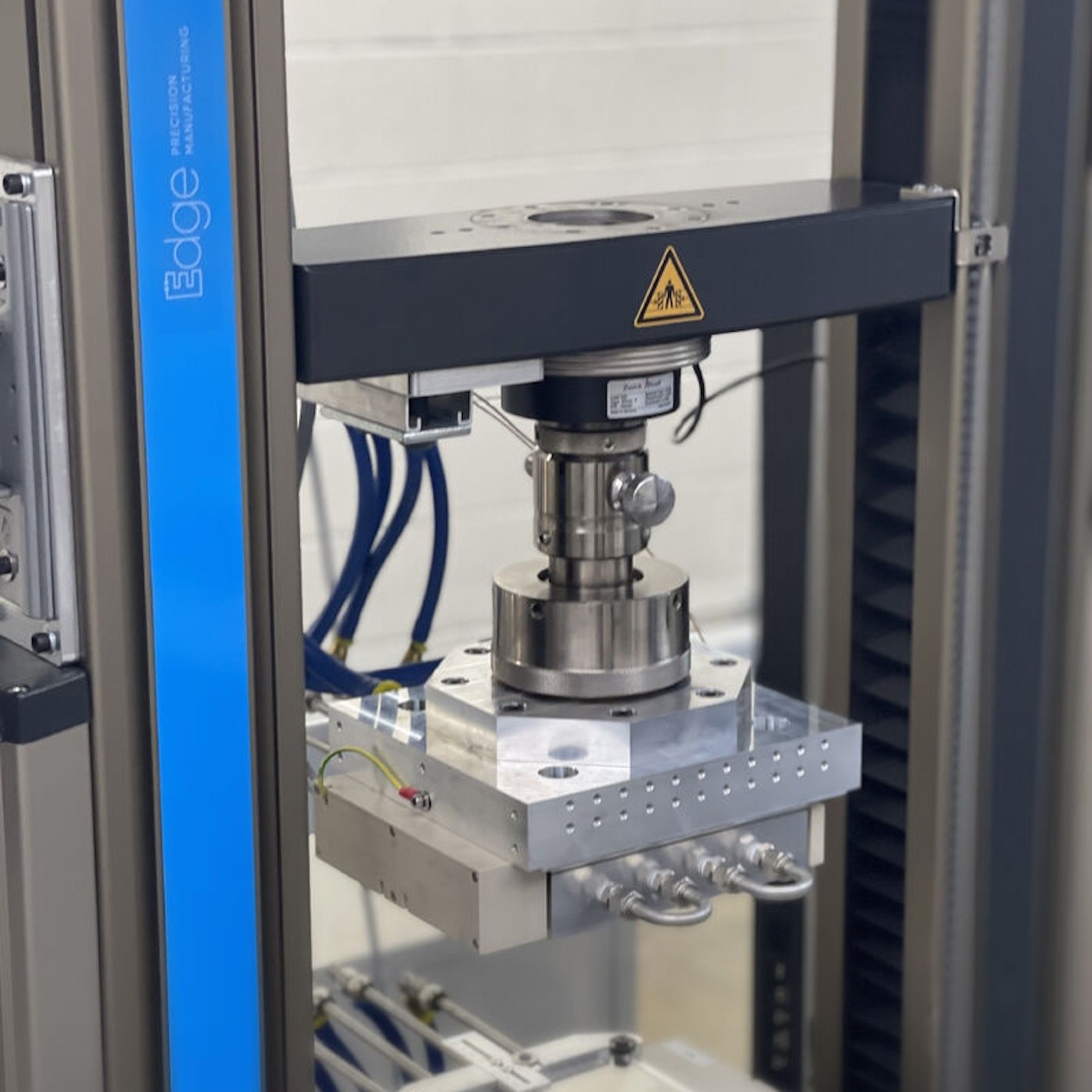
Parallelized single-cell and bead device for drug discovery applications
An Edge customer provides service-based programs to large pharmaceutical clients.The customer offers an internal platform consisting of a massively parallelized single-cell and bead device used in drug discovery applications. The device uses Poisson-style distribution of cells and nanobeads into precision microwells with micron-scale tolerances and alignment.
A trusted vendor to the customer, Edge produces parts within its ISO Class 7 clean manufacturing facility as part of an ongoing supply agreement.
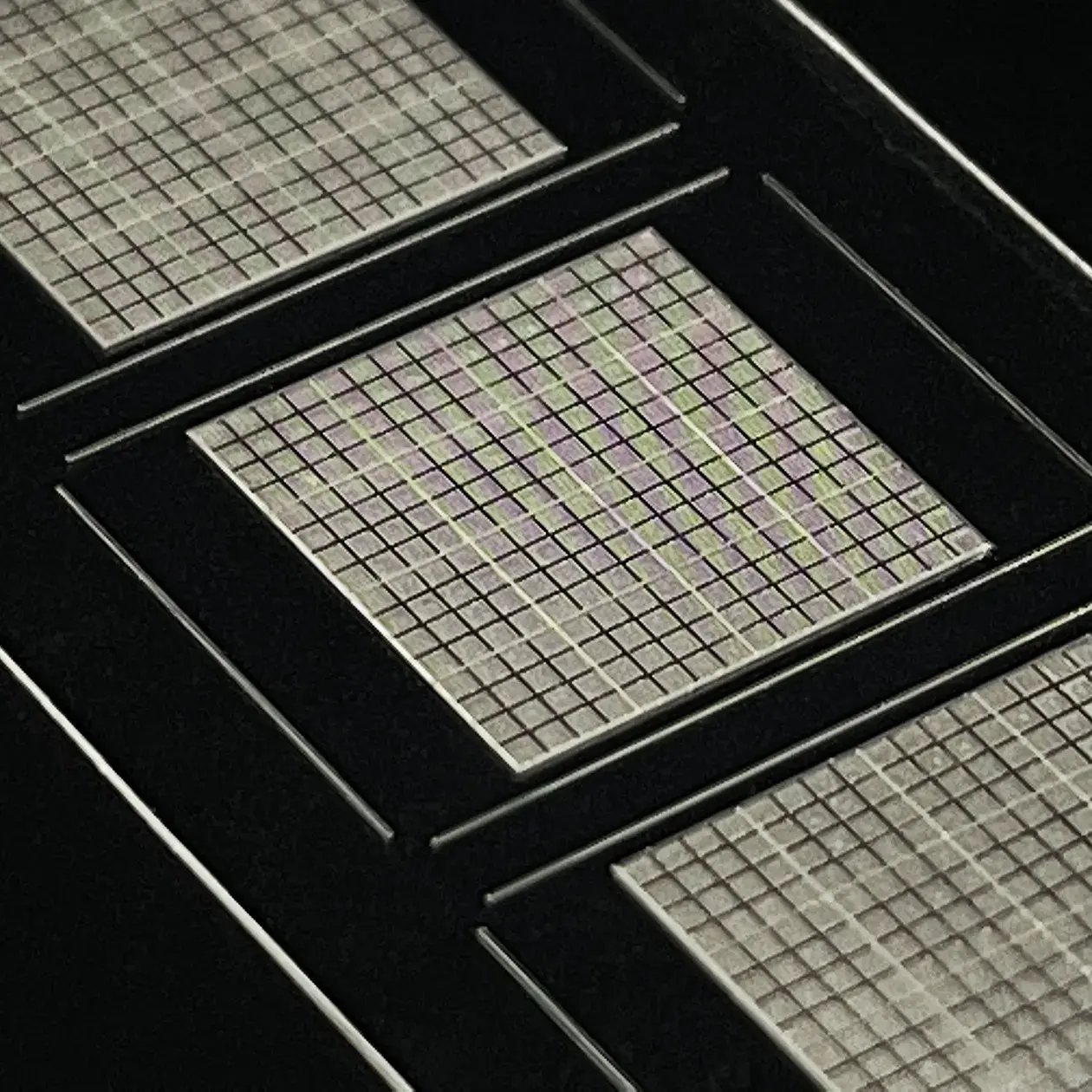