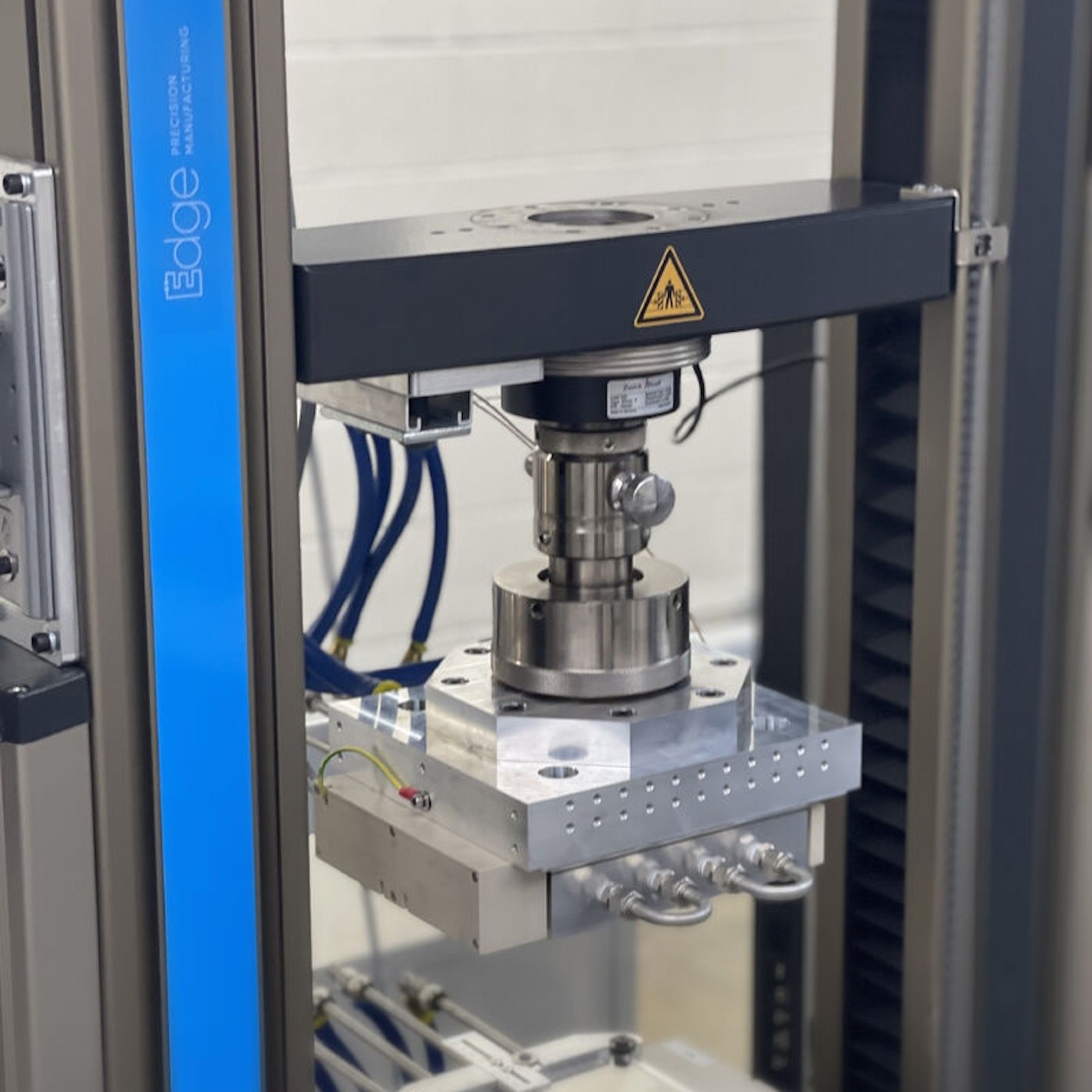
Compression Molding
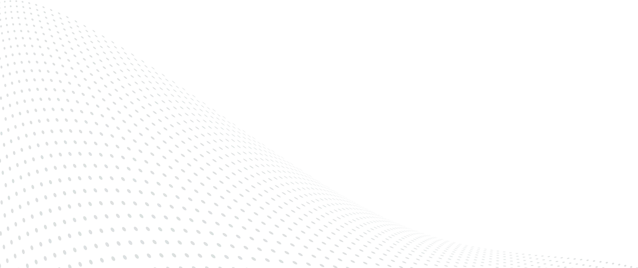
Edge's patented thermal compression molding process enables the manufacture of superior disposables with best-in-class optical properties and unlimited combination of microscale and macroscale features
Edge utilizes our proprietary tooling technology to provide several technical benefits that can’t be achieved in plastic parts with other processes:
- Low birefringence, low background fluorescence, and optical surface finish
- Microfeature geometry tolerances held to hundreds of nanometers
- Design flexibility to achieve highly variable wall thickness and other features without defects common in injection molding
- Fastest time to product quality parts; our process and materials are the same regardless of volume
- No cavity-to-cavity variation
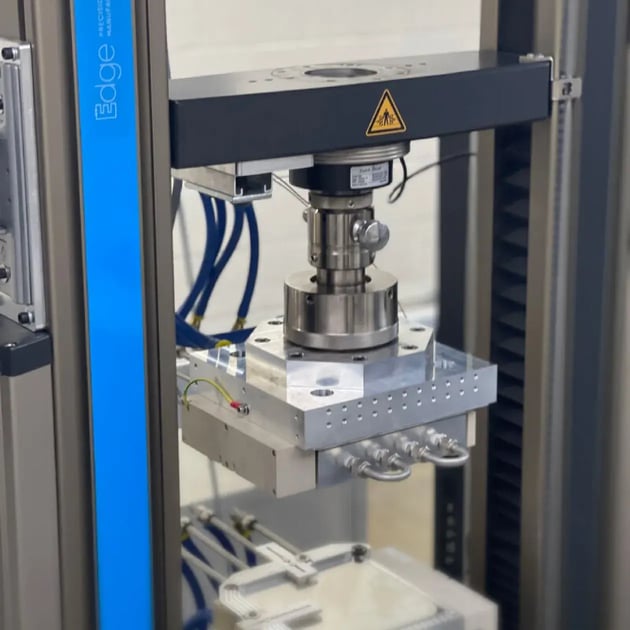
Technical capabilities
- 8 custom-built thermal compression molding presses
- Parts up to 130 mm by 130 mm footprint with thickness ranging from 100 µm to >5 mm
- Minimum feature size of 1 µm (sub-micron in some cases)
- Monolithic combination of micro and macro features
- Part flatness as low as 1 µm thickness variation over linear centimeter
- Contiguous services for assembly, lidding, and packaging
- Contiguous full inspection suite using confocal microscopy, digital microscopy, and more
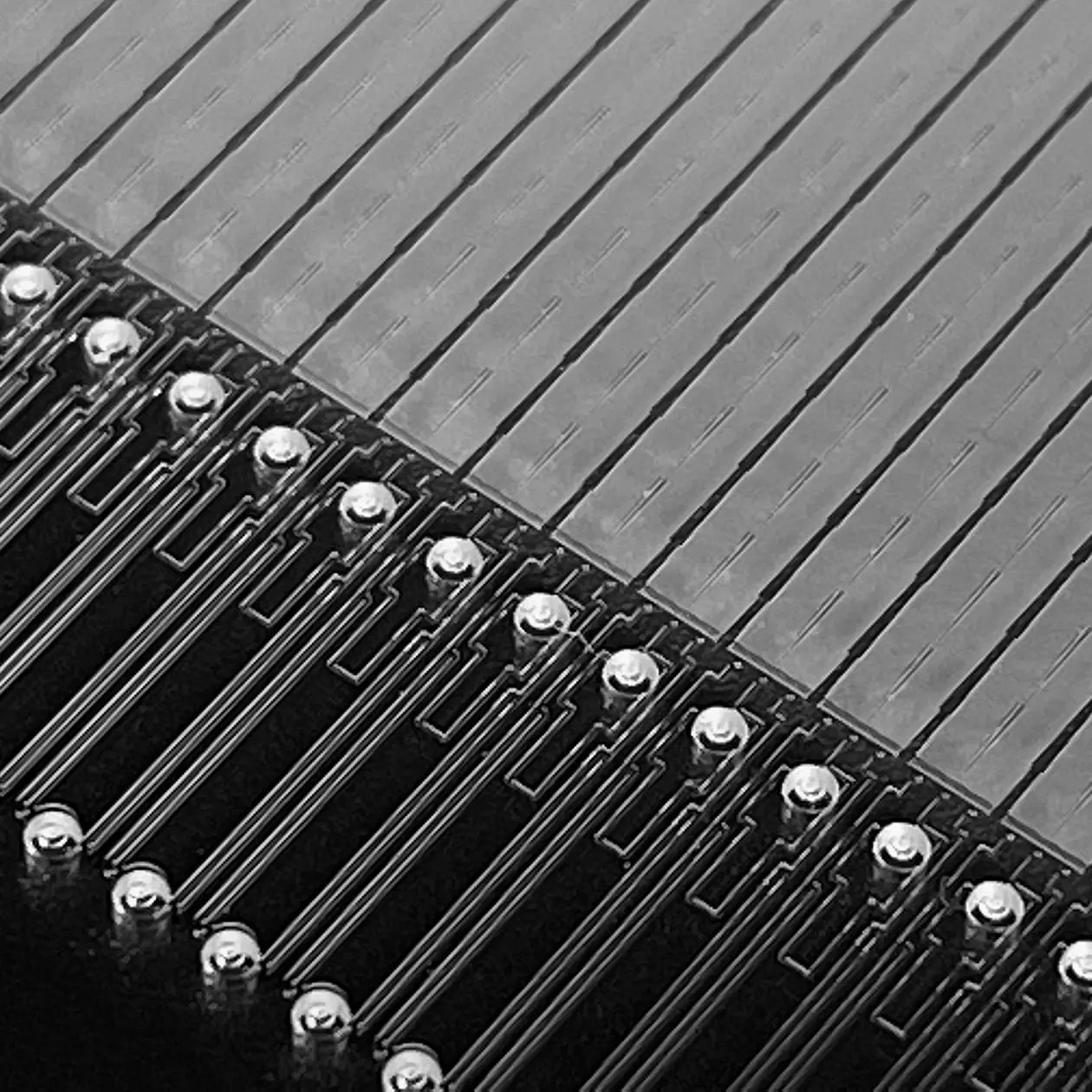
Facility details
- Molding, bonding, assembly, and packaging integrated into Class 7 (10,000) clean room
- ISO 13485:2016 compliant
- Capacity over 1 million pieces per year
- Technology developed at Edge over 20+ years
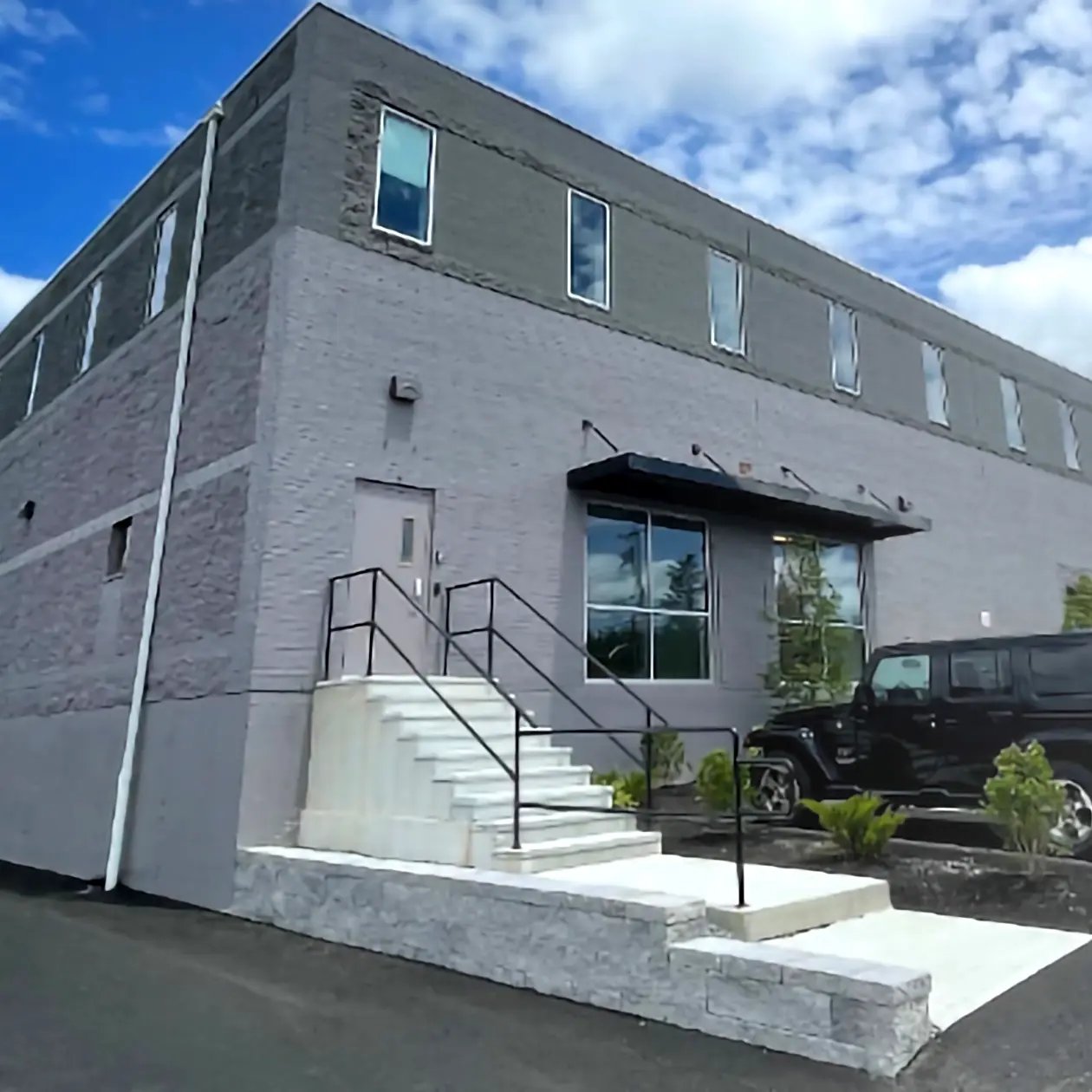
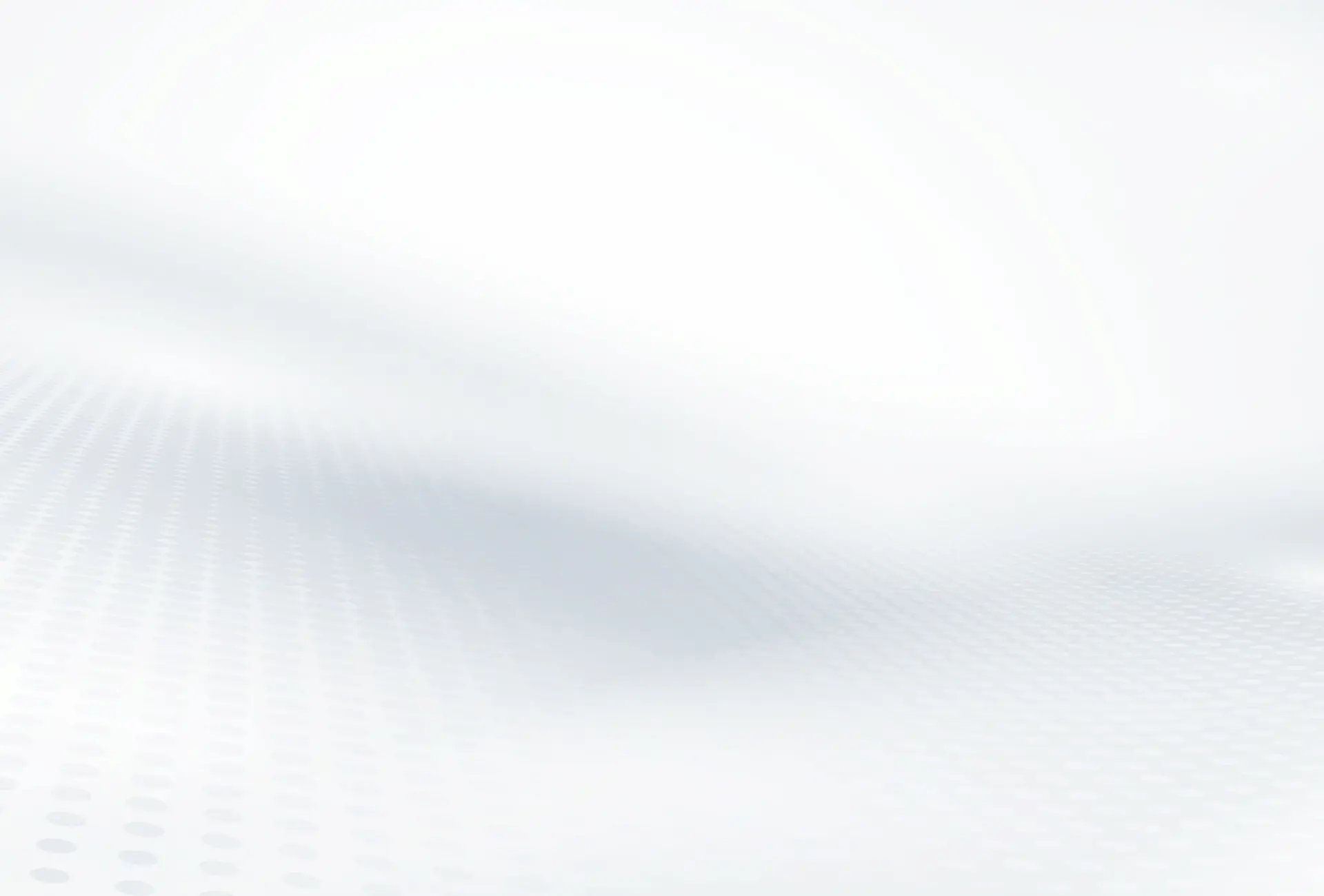
Technical Highlights
No common molding limitations
- No ejector pin marks
- No gate vestiges
- No knit lines
- No flash
- No draft
- No residual stress
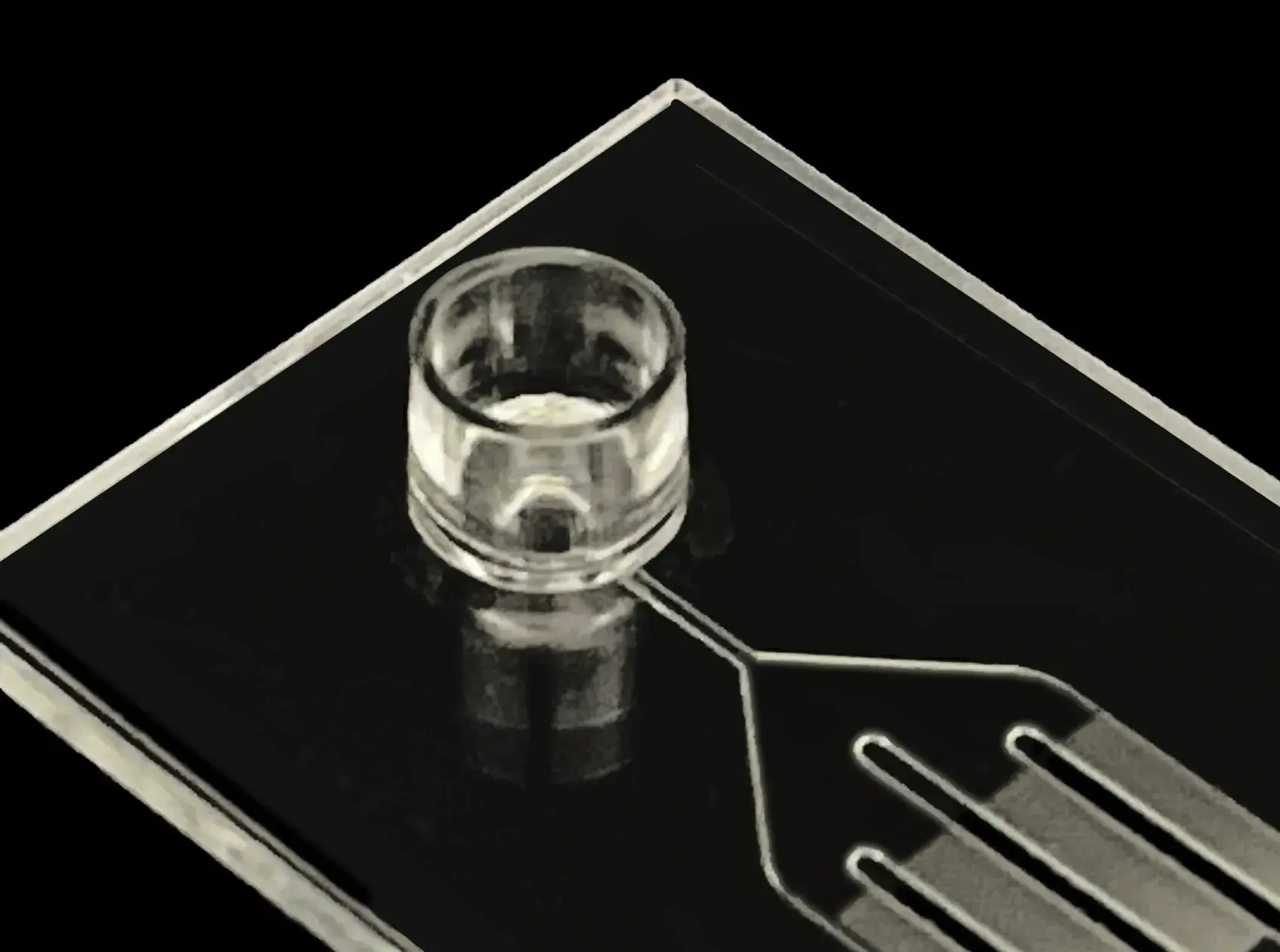
Product-quality parts from the start
From feasibility samples through high volume production, our process and materials remain the same. This ensures equivalent product performance with every part we manufacture.
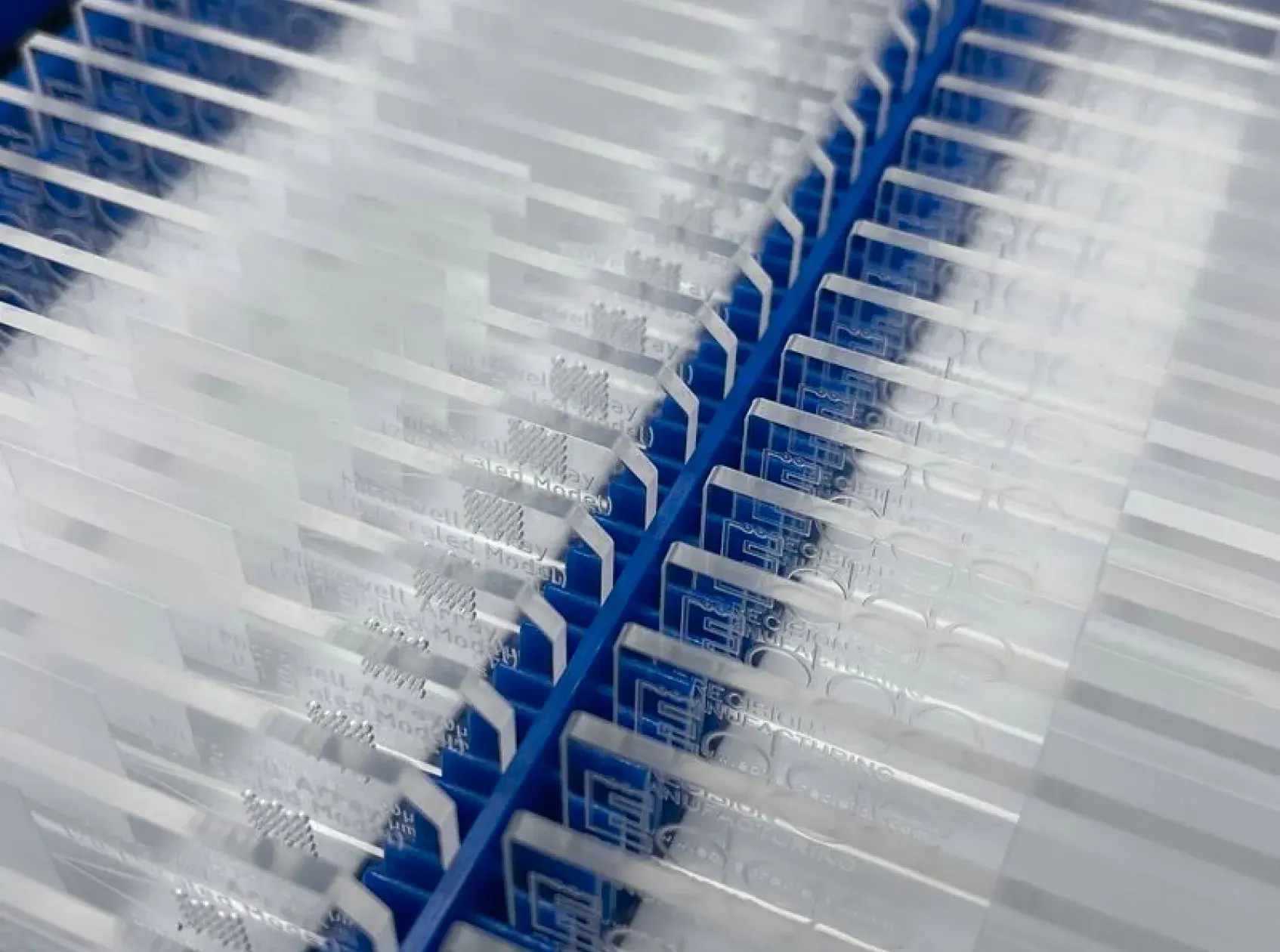
Supply assurance
Our molding technology ensures that there will never be an interruption in the supply of parts.
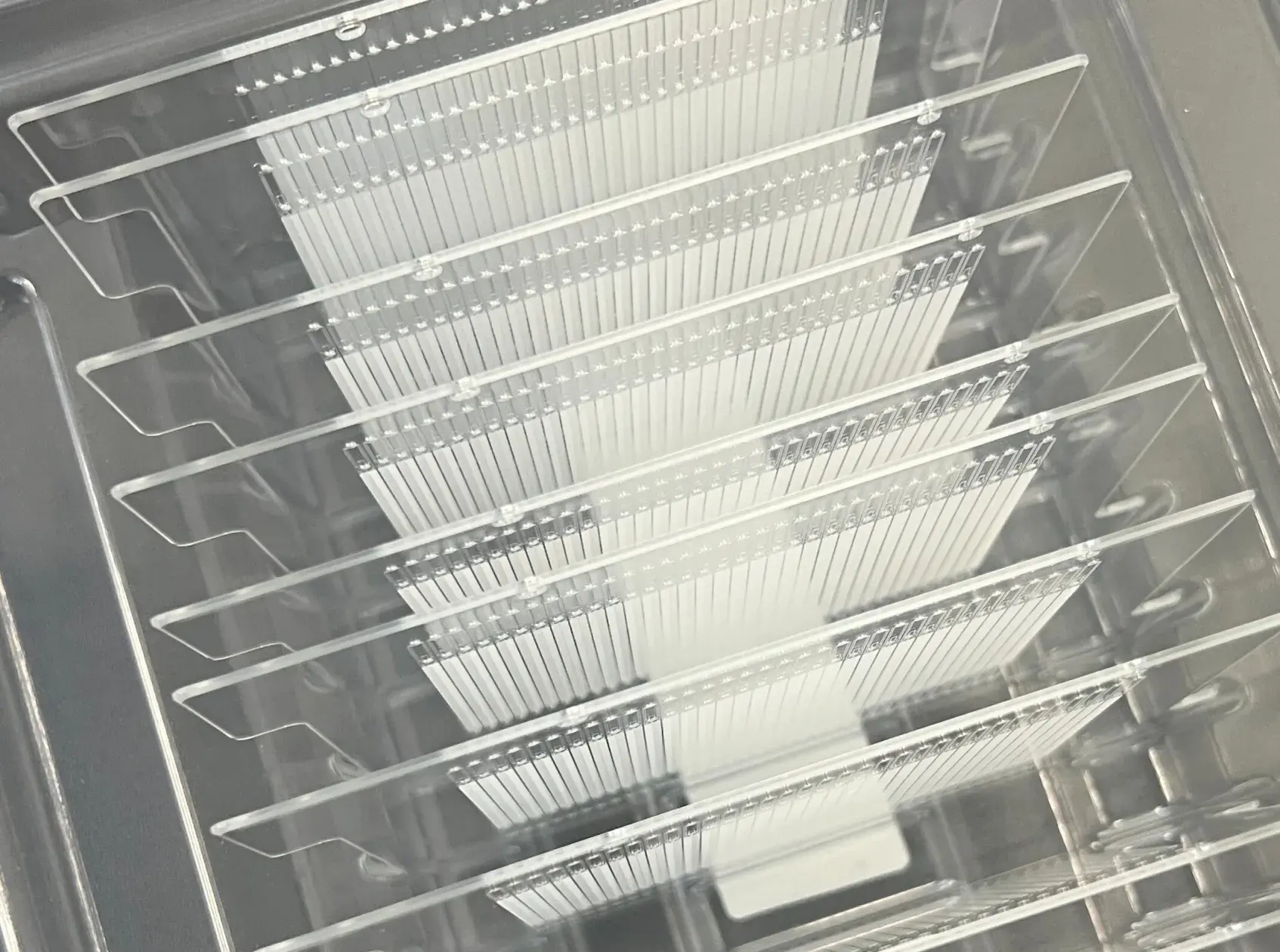
No cavity-to-cavity variation
Our technology creates exact copies from cavity-to-cavity from tool-to-tool. Tolerances are measured on a micron or sub-micron scale.
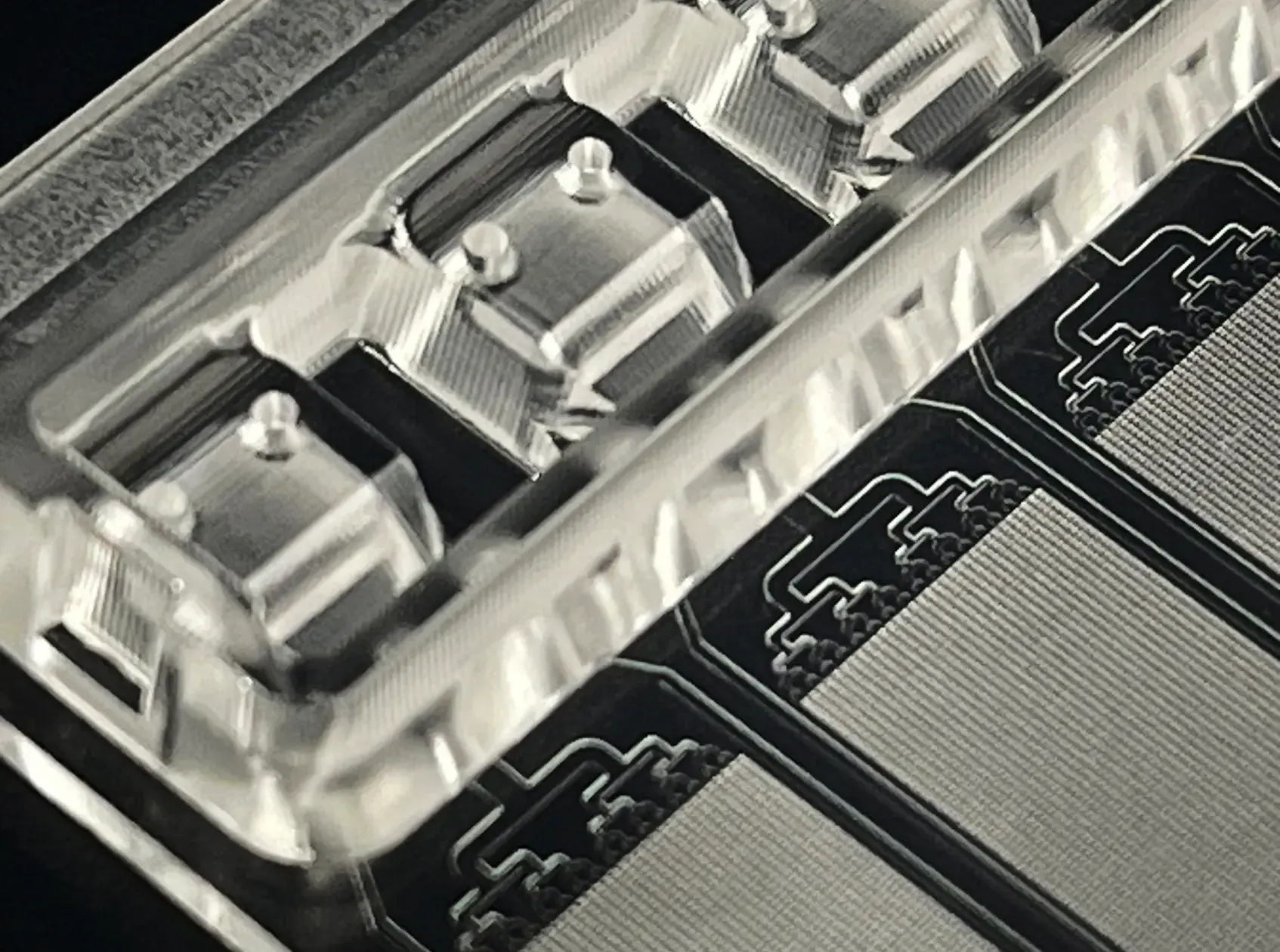