Compression-molded COP and other plastics offer an alternative to glass with similar optical properties
Glass is often the first and only material considered for medical, diagnostic, and optical devices requiring high light transmittance, low background fluorescence, and low birefringence. However, advances in optical-grade plastic—driven by the market for highly shapeable, transparent material in eyeglasses, electronic displays, and cellphone cameras—have made plastic a viable choice in many devices that once required glass components. For many applications, optical-grade plastic is the best and most economical choice for devices with complex geometric structures incorporated into a single part.
Plastic parts for optical devices are not new. For decades, labs have used optical plastics in spectrophotometry, qPCR, dPCR, and microscopy. These kinds of routine, workhorse uses have traditionally seen the most benefit from plastic—a flexible, moldable material that’s inexpensive enough for single use applications.
Applications requiring the absolute best in optical performance, however, have traditionally relied on glass. For example, when gathering the perfect microscopic images for publication, the additional expense and fragility of glass coverslips are acceptable tradeoffs. The tradeoffs grow, however, when using optical glass for devices requiring more complex surface geometry. In detailed parts, etched glass and glass capillaries may still provide the highest optical performance, but the production cost will be prohibitive in most cases.
Improved optical performance of plastic, however, means that more applications are candidates for a switch from glass to plastic. Our experience at Edge Precision Manufacturing has shown that the right choice of plastic can even match other application-critical characteristics of glass, such as its durability, chemical resistance, biocompatibility, and broad range of sterilization options—all while overcoming glass’s limitations. In many cases, switching to plastic can lower production costs with no hit to performance.
Limitations of Glass
Glass cannot offer the flexibility and price-competitiveness of plastic parts. Glass’s limitations include:
- High cost compared to most optical-quality plastics
- Complex assembly processes involving bonding steps which require their own development cycles
- Feature design limitations related to geometry
- Housing design limitations related to drop test requirements
- Additional packaging requirements due to the need to ship glass
- Lack of durability that may be incompatible with medical devices
Glass-like Optical Properties Available in Plastic
Advances in plastic materials and processing allow Edge to offer a range of compression-molded plastic options. ZEONOR® and ZEONEX® cyclo-olefin polymer (COP), cyclo-olefin copolymer (COC), polystyrene (PS), polycarbonate (PC), and polymethyl methacrylate (PMMA) from Edge offer glass-like optical properties suitable for many devices.
Transmittance
Transmittance through 3mm glass is typically above 90% across the visible spectrum (380-700nm), with some optical-grade glass materials offering nearly 100% transmittance. Applications requiring the highest possible sensitivity may therefore require transmittance performance found only in glass.
Many analytical and diagnostic devices, however, don’t require perfect transparency. Even when high sensitivity is required, plastic can approach the transparency of glass, with select optical-grade plastics achieving 90% transmittance through 3mm. Edge molds parts in plastic materials that can meet the transmittance requirements for most applications.
Edge parts also replicate the surface finish typically associated with glass optical components, thus minimizing light scatter. Compression molding reproduces the surface smoothness of the mold, right down to the nanoscale, ensuring that a glass-like optical surface finish is present from prototype to finished part.
Transmittance curves through 3mm plate of a popular optical plastic offered by Edge. Transparency approaches 90% across the UVA spectrum (315-380nm) and is at or above 90% across most of the visible and much of the near-infrared spectrum (380-1100nm).
Edge compression-molded COP parts are available with a surface finish typically associated with glass optical components.
Fluorescence Background
Low background fluorescence is crucial for maximizing sensitivity in cytometry, fluorescent imaging, qPCR, and dPCR. High quality optical glass is ideal for these applications, because its background fluorescence is low to undetectable in most cases.
Some varieties of plastic, such as polystyrene (PS), display high levels of background fluorescence. However, low-fluorescence plastics, such as COP, feature fluorescent background that’s low enough for detection, quantitation, and imaging applications.
Edge plastic parts made from the ZEONOR® COP family of materials offer the lowest background fluorescence of any available molded plastics. ZEONOR’s fluorescence properties show almost undetectable levels of fluorescent background in visible light (380-750nm) and near infrared (750-1400nm), and very low levels of fluorescence background in UVA (315-380nm).
ZEONOR® COP may show limited background fluorescence when using dyes that excite at lower wavelengths, such as Alexa Fluor® 350, some varieties of Qdot™, and Brilliant Ultra Violet™ dyes. This may slightly raise the limit of detection when using these dyes. When using common fluorophores like GFP, CFP, RFP, PE, APC, FITC, and most Alexa dyes, though, ZEONOR® COP’s background fluorescence is almost identical to glass.
Compared to the high background fluorescence in PS, ZEONOR® COP exhibits excellent characteristics, making it an appropriate choice for most fluorescent detection and quantitation applications.
Birefringence
Plastics are sometimes ruled out in optical devices due to concerns about birefringence. Injection molded plastics can suffer distortion due to birefringent artifacts, creating problems in cell culture automation and other applications that involve microscopic imaging in the visible spectrum—particularly when imaging through a polarized filter.
This does not, however, make glass an absolute requirement for these applications. The choice of molding process plays a large role in plastic birefringence, with injection molding showing the most severe birefringence. This is due to stresses on the part caused by uneven cooling after fabrication. Compression-molding produces less stress, and Edge has refined the cooling process to reduce it even further. Combined with a material that has intrinsically low birefringence, such as ZEONEX COP®, Edge can therefore achieve some of the lowest birefringence available in optical plastic parts.
The use of low-birefringence material, compression molding, and controlled cooling allow Edge parts to exhibit a near-complete lack of birefringence-related artifacts.
Advantages of Plastic
In addition to approaching the optical performance of glass, Edge’s proprietary compression molding techniques produce plastic parts with advantages that glass can’t match.
These include:
- Significantly lower cost
- Higher manufacturing capacity
- Macro, micron, and sub-micron scale features can be included easily
- Extremely thin part sections that would not be economical to fabricate in glass
- Up to a 10:1 ratio of thickest to thinnest feature
- Eliminating many other design constraints found in glass
- Mechanical flexibility, especially compared to the high rigidity of glass
- Low protein adsorption, low nonspecific binding, and low sample loss in COP & polypropylene (PP)
Other Glass-Like Qualities Available in COP
For optical applications which require them, Edge COP parts can also match many of the favorable, non-optical characteristics of glass.
Edge COP parts are:
- Plasma-treatable
- Ideal for surface-functionalization in applications that require high binding of proteins, antibodies, or cells
-
- A suitable substrate for self-assembled monolayers (SAMs)
- Moisture-impermeable, and will not pick up water as occurs with polymethyl methacrylate (PMMA)
- Sterilizable by gamma radiation, electron beam, ethylene oxide gas, and single-cycle steam autoclaving (with some reduction in tensile elongation resistance when autoclaving)
- Solvent resistant to limited contact with nonpolar solvents and hydrocarbons, especially in COP
- Biocompatible
- Inert to most lab reagents
- Pharmacopoeia-listed for pharmaceutical storage, implantation, and injection
Optical-Grade Plastic May Be the Best Fit for Your Applications
Although not a match for every use case, plastic parts are comparable to glass for many optical applications, at a fraction of the cost. Edge compression-molding techniques provide additional advantages that enhance part functionality and provide a wider range of design options compared to glass.
If you’re looking to reduce costs and capitalize on the other benefits of optical-quality plastic parts, we’d be happy to discuss your device needs.
Contact us to talk about your optical requirements
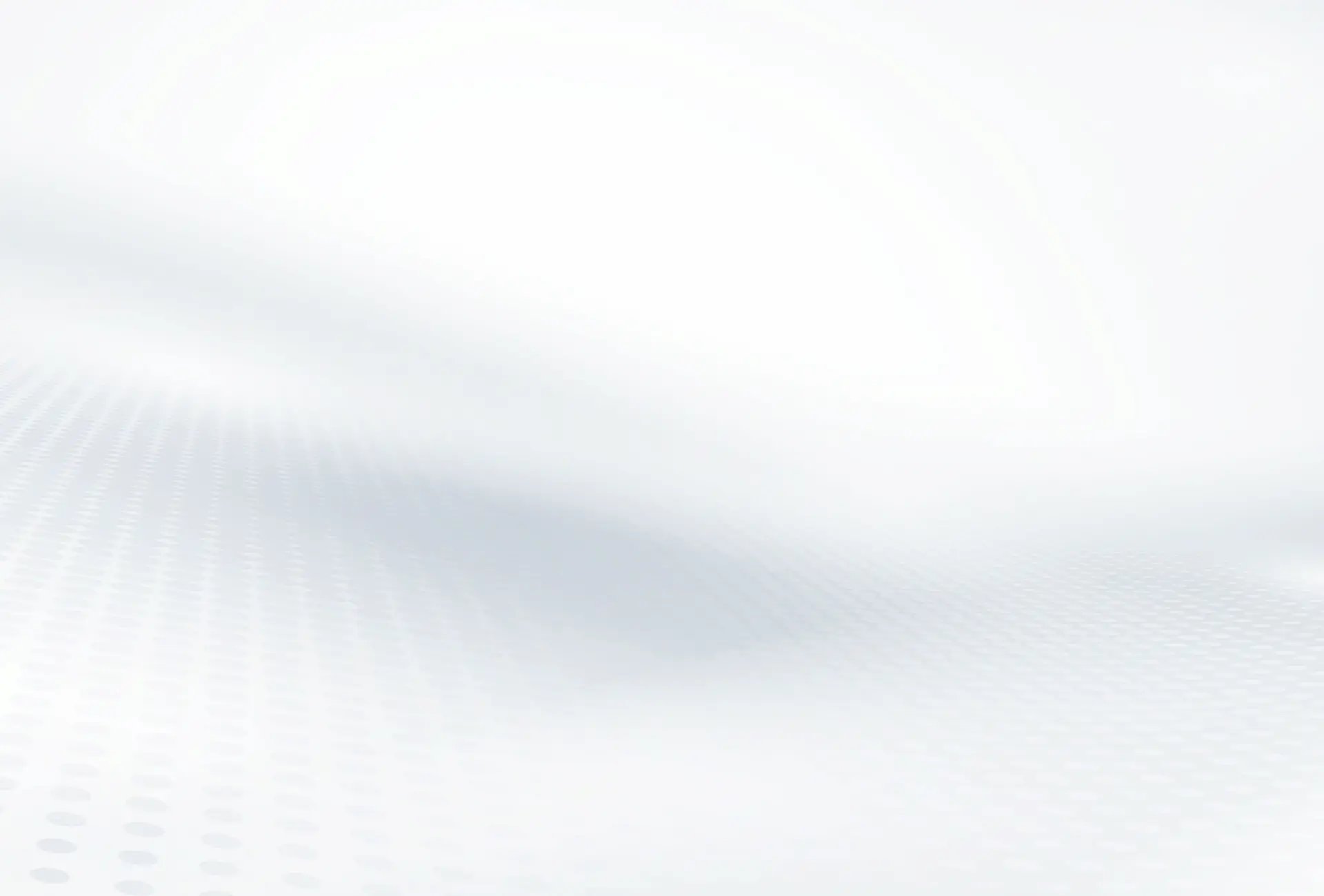
The Latest From Edge Precision
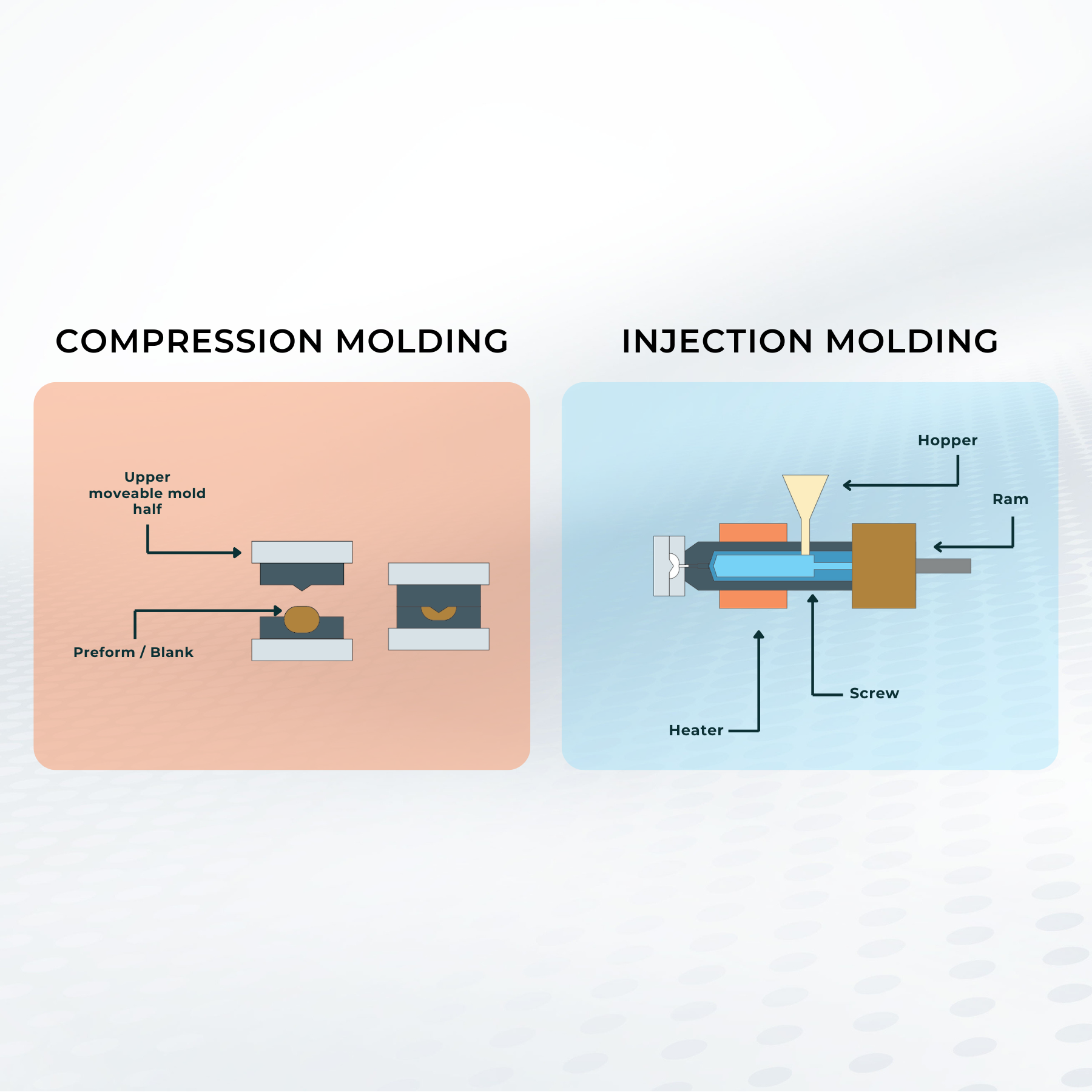
Is My Application a Good Fit for Edge's Proprietary Molding?
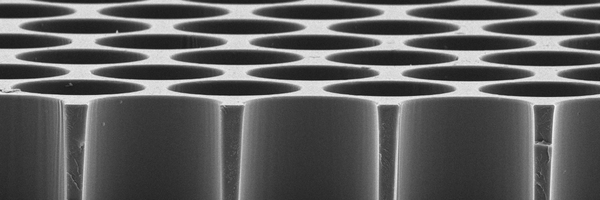
Next-generation microwell and nanowell arrays for single-cell applications
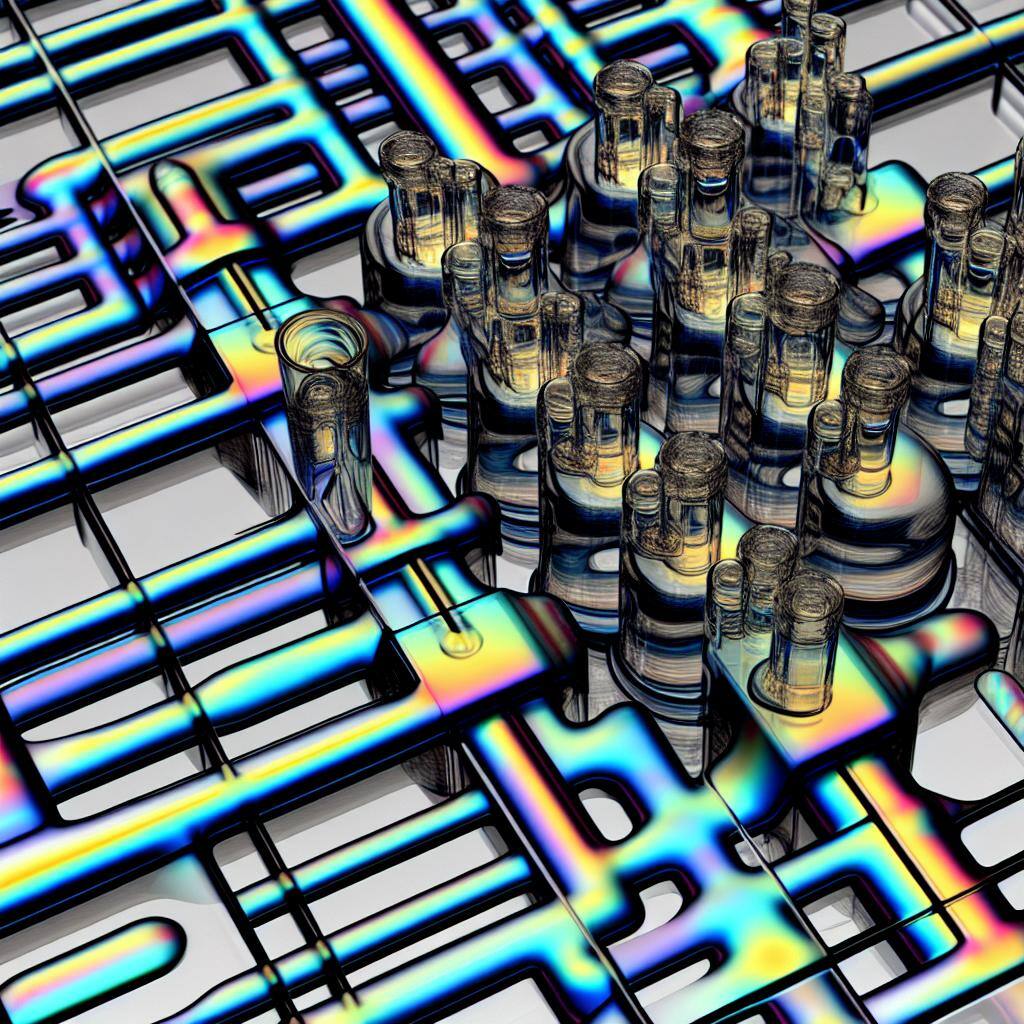