Is my application a good fit for Edge’s proprietary molding
technology?
Edge offers device manufacturing solutions that provide the best of both worlds: price optimization on thermoplastic parts without the design-restrictions of injection-molding—all on a fast timeline.
How Edge’s proprietary methods compare to injection molding
While most plastic parts are manufactured by injecting molten plastic into a mold, Edge compression-molded parts are formed from a plastic blank under precision-controlled temperature and pressure conditions optimized to maximize consistency and provide the most versatile range of features at low cost.
Edge’s compression molding process:
Our process is an advanced and proprietary form of thermal compression molding. At its core, compression molding utilizes a set mass of thermoplastic, which is heated in place and formed using applied pressure. Because Edge’s process fully heats and then cools during each cycle, molded parts are thoroughly annealed, thus containing virtually no residual stress. Edge’s proprietary tooling method results in easy ejection of molded shots, even when they contain zero draft, high aspect ratios, or microscale features.
Applications that benefit from Edge’s innovations in low-cost, high-precision plastic parts:
Categories of Devices that Benefit:
- Medical disposable devices
- Molded optical quality components
- Custom SBS format wellplates
- Thin microfeatured films
- Microfluidic components
- …and many more
Specific Applications Include:
- Drug discovery and delivery devices
- Sample-to-answer devices
- Point of care testing (POCT)
- Blood separation and other bulk cell sorting
- Single-cell capture
- Microfluidic cell culture
- Lab-on-a-chip devices
- Microfluidic cytometry
- Fluorescent interrogation and characterization
- Imaging and other optical detection
- Flow control devices
- Companion diagnostics
Edge may be the best solution if your plastic device requirements
include:
Strong, Stress Free Parts
Edge's compression molding technology produces parts without knit or flow lines and also does not use ejector pins. Resulting parts have very high structural stability and near-zero internal stresses. This means they start flat and stay flat, even when subjected to secondary processes such as laser welding, ultrasonic welding, or thermal bonding.
Micron-scale features
Edge has adapted the tools and methods used in micron-scale fabrication to achieve higher precision than is possible with traditionally manufactured plastic parts. This allows Edge to manufacture parts with features down to micron and submicron sizes.
High part-to-part consistency
Our mold replication methods hold process precision to within 1% of feature size in multi-cavity tooling and even across multiple tool sets. That means parts perform predictably, and device performance is identical across all parts and production runs.
Large, thin components
Our process starts with a solid blank which is then formed into a mold using uniform heat, compression, and vacuum conditions, so Edge can manufacture large, thin features that would otherwise require redesign or additional assembly to avoid short-shot conditions.
No warp or deformation
Meticulous control of the cooling cycle relieves internal stress in Edge’s plastic parts to almost immeasurably small levels. As a result, Edge’s parts maintain their precise dimensions, without the stress-induced warping and deformation inherent to other molding processes, extending both the use life and shelf life of the device.
Combined macro & micro features
Our compression molding technology, developed over 18+ years in business, allows us to seamlessly combine both macro and micro features on the same part.
Specific plastic properties
A versatile process allows Edge to work with a wide variety of plastics, including high-quality USP Class VI thermoplastics. Our experienced team will guide you through selection of a plastic with the optimal mix of mechanical, biological, chemical, thermal, and optical properties for your requirements and specifications.
Optical versatility
Molded plastic parts from most manufacturers are incompatible with imaging and fluorescent detection, due to their optical properties. Select materials available with Edge’s molding methods, however, feature low birefringence, reduced internal reflection, and minimal background fluorescence, making Edge parts ideally suited to these applications.
Parts without common molding limitations
Parts manufactured by Edge have no gate vestiges, ejector pin marks, knit lines, or other artifacts common to traditional molding techniques. In addition to giving Edge parts a cleaner appearance, this means there is no need to make engineering compromises based on tooling limitations. Common assembly issues related to those limitations are also avoided.
Zero draft angle
While most plastic molding methods require a draft angle on features with a high aspect ratio, to facilitate release from the mold, Edge’s proprietary methods can render micron-scale features with a 0° or even slightly negative draft angle. This makes Edge devices better suited to cell sorting and other microfluidic applications.
Production-quality parts in 6 weeks
Due to difficulties inherent in generating production-quality tooling, most plastic parts manufacturers use cheaper, simpler fabrication methods for prototyping and design finalization. Edge’s molding technology does not differentiate between prototype tooling and production tooling, so production-quality parts are produced even at the prototype stage.
Product launch in under 6 months
Because Edge’s tool fabrication, molding method, and materials are identical in both prototyping and production, the path to product launch is streamlined. Additionally, our ability to manufacture parts using family tools with non-uniform wall thicknesses allows greater flexibility in design, leading to a timeline that’s as short as 24 weeks.
Contact us to discuss your project needs.
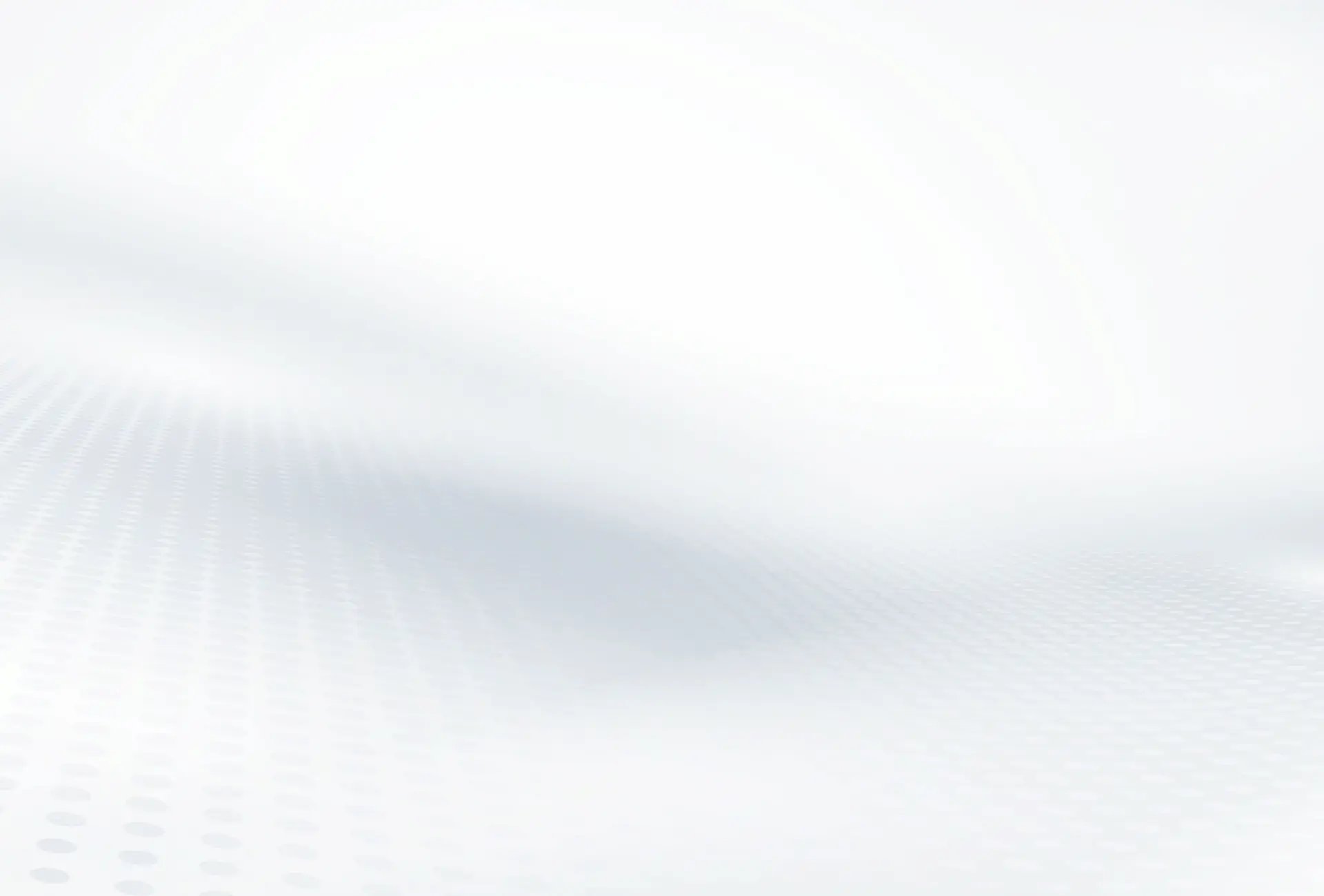
The Latest From Edge Precision
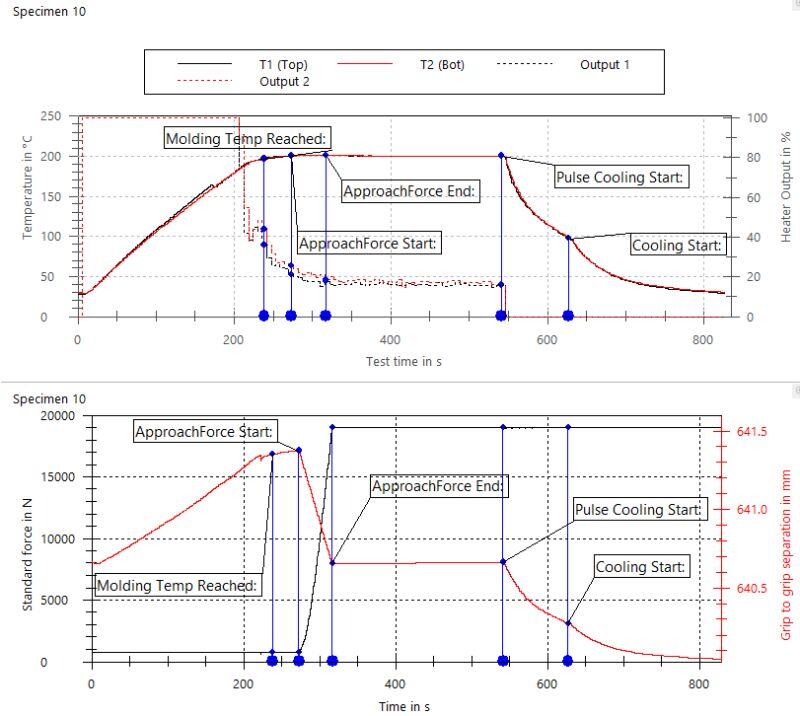
Achieving superior quality in molded plastic parts: Edge's advanced compression molding process
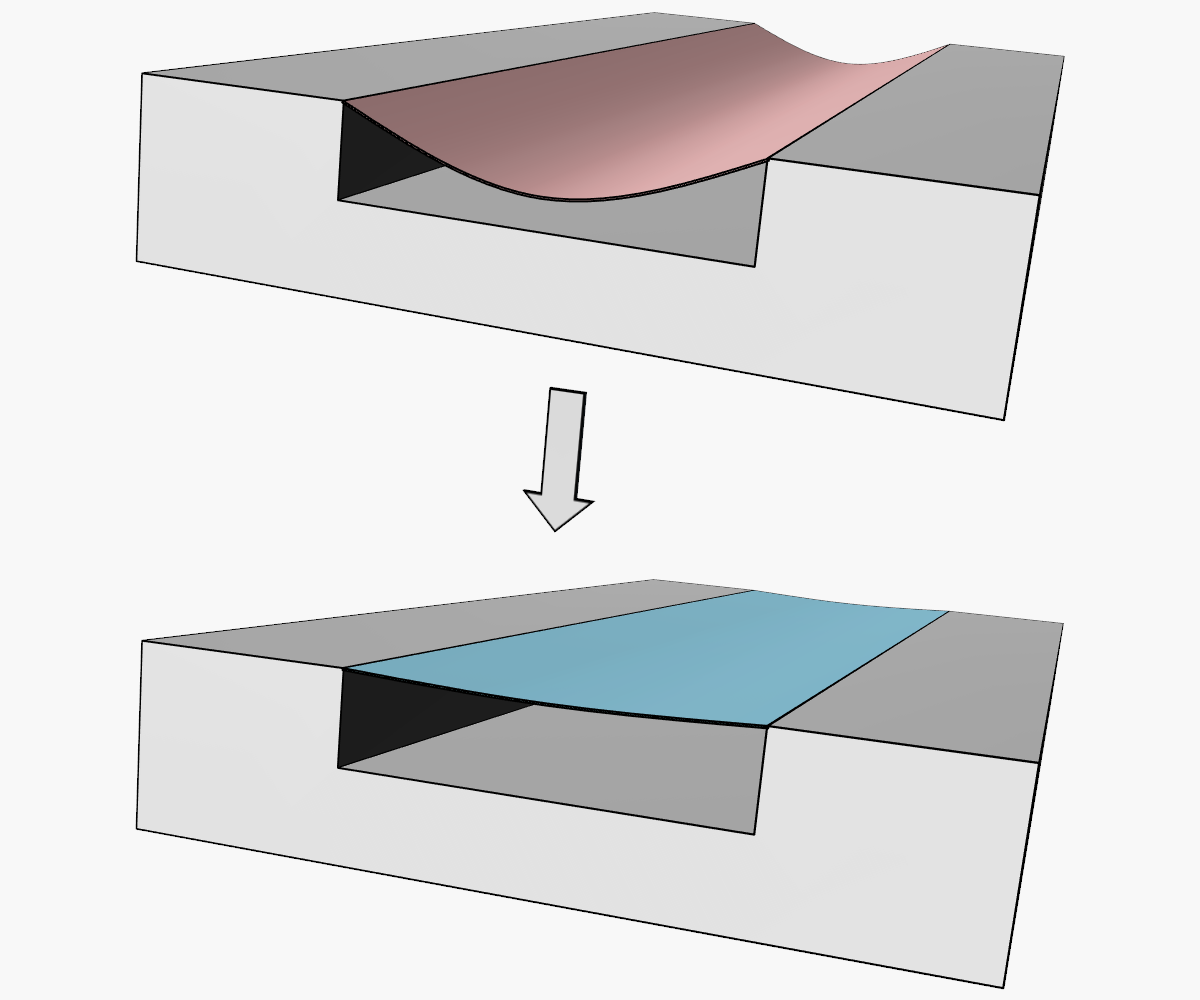
EdgeBond: Thermoplastic Bonding for Microfluidics with Minimal Feature Distortion and Lid Sagging
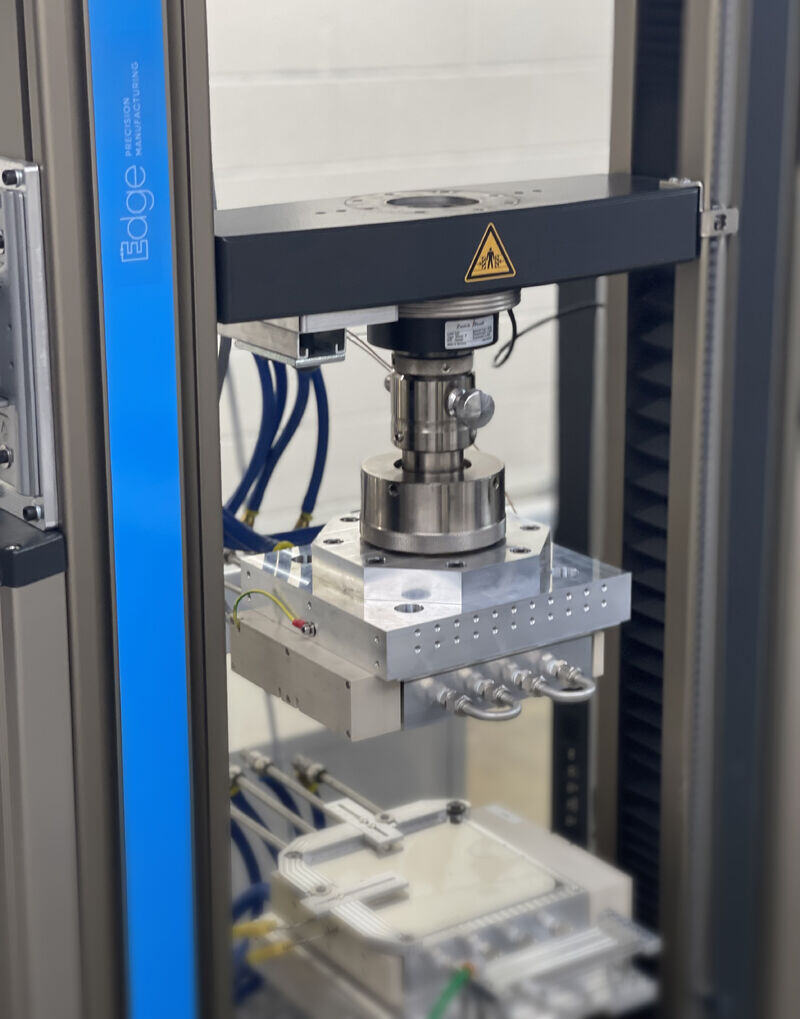